Starfish is a control board built around Raspberry Pi’s RP2040 chip and designed as the central nervous system for a pick and place machine. Pick and place machines are precision robots which build other things more efficiently than humans.

Thea (aka Stargirl Flowers) decided to dive right in and design her own board to power a LumenPnP she made last year.
Special requirements
Starfish performs most of the same actions that a 3D printer control board does, but with a few added requirements such as vacuum sensor communication and solenoid control. The robot-like arm parts are pneumatic, and vacuum control solenoid valves give them their ability to pick things up and put them down in a controlled manner by managing the release of air at the right time. The board also controls a NeoPixel ring light for the machine’s camera, as well as a gazillion external peripherals requiring 5V power.
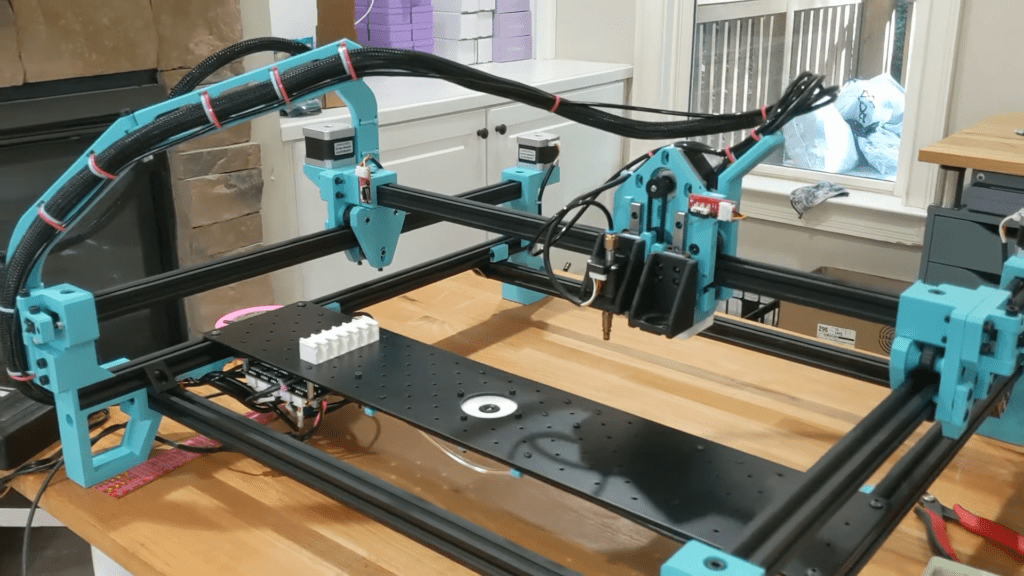
Starfish uses USB to connect to the pick and place machine and receive commands, and RP2040 is the brains of the board. The maker explains she chose RP2040 to handle all the digital peripherals that the board has to talk to due to its “abundance of digital I/O.” A perfect fit.
Thea has compiled perhaps the most comprehensive and easy-to-read project guide I have encountered. Have a scroll through if you’d like lots of detail on the power source, stepper motors, pumps, schematics, and more. Starfish is completely open source, with files available on GitHub.
Meet the pick and place machines that make Raspberry Pi boards
You can watch the pick and place machines at the SONY factory in Wales where Raspberry Pi boards and accessories are assembled and packaged in our timelapse video. I’m sure you’ll agree they would be 83% better with googly eyes.